· articles · 5 min read
The Working Principles of Gas Mixers
Gas mixers are used in many industries to generate a controlled amount of each constituent gas to form the desired blend
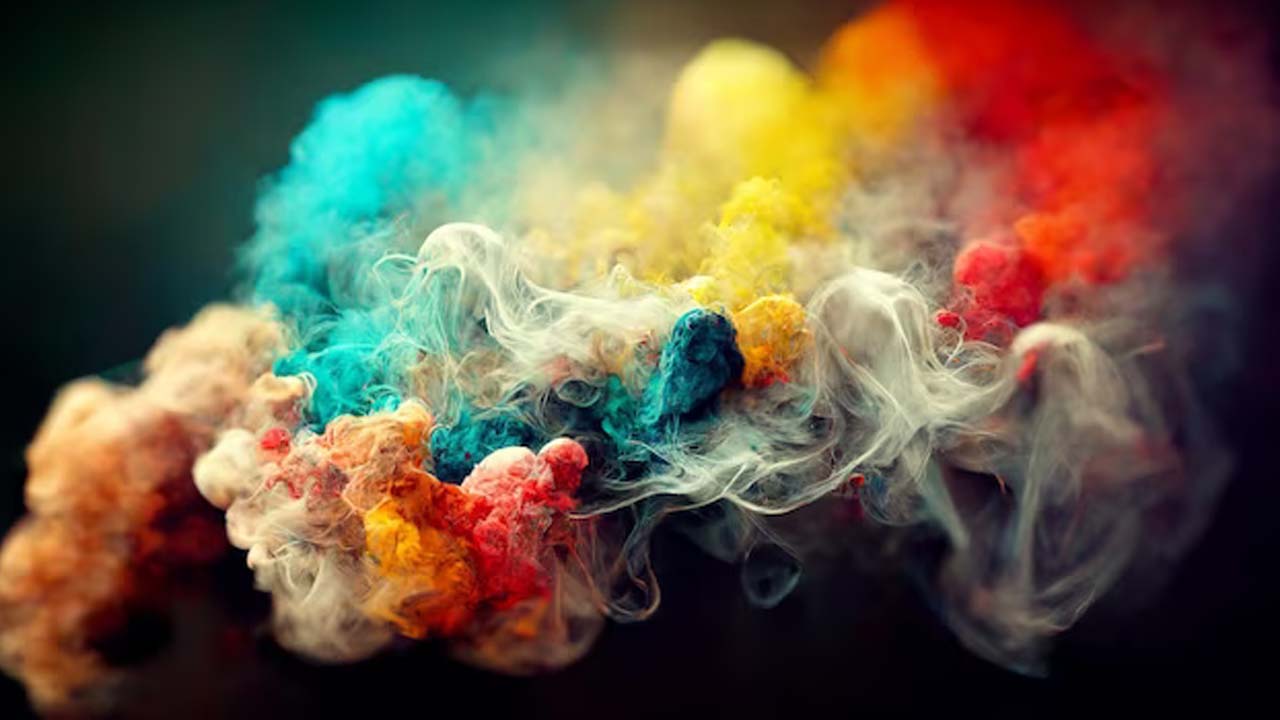
Countless industrial processes, consumer applications, and areas of academic study require finely-tuned gas mixtures in order to guarantee their success. Typically, these gas mixtures are either batch-produced commercially, or generated locally from available pure gas feed stocks; as required by the application. In both cases, an accurate gas mixing system is essential in creating a reliable and consistent gas composition for use in the end user’s process.
The Role of Gas Mixers
Before outlining the working principles of gas mixers, it is worth exploring their roles in different markets. For example, recreational and commercial underwater diving outfits both utilize carefully balanced ‘non-air’ breathing gases in their SCUBA tanks. These mixtures are used to improve the divers’ respiration physiology while underwater and combat the risk of decompression sickness.
Gas mixers are used to feed the compressors that fill breathing gas tanks with an oxygen enriched breathing gas, known as Nitrox or EAN. While 32% O2/68% N2 (EAN-32) is in widespread use, higher O2 percentages are often useful for specific applications. It is not uncommon for commercial diving operations to have air separation plants (typically a pressure swing adsorption ‘PSA’ system) on-board, so that the custom Nitrox blends may be generated right on the boat.
In the Industrial Sector
In the industrial sector, gas mixers are most commonly used to facilitate welding or cutting processes. For example, both metal inert gas (MIG) and tungsten inert gas (TIG) welders use quite a wide variety of inert and active gas mixtures, depending on the thickness and composition of the workpiece. While the most common mixtures for the MIG process are a blend of argon (Ar) and carbon dioxide (CO2), the ideal ratios for any given alloy or thickness varies widely and is often the subject of debate. If multiple commercial blends are needed for process development, the logistics can become arduous and the cost high. Modern fabrication plants solve this problem by using in-house gas mixers. These mixers provide variable, precise multi-gas mixtures at controlled pressures or flows.
In the Food Industry
Gas mixers are also used in the food industry to help prolong the shelf lives of perishable goods by controlling the gas composition within modified atmosphere packaging (MAP). Dozens of commonly used MAP gas mixtures are most economically produced on-site from pure gas feed stocks. The use of a carefully controlled high pressure distribution network allows the individual packing stations to have improved cost effectiveness, and the flexibility to easily switch from one type of food packaging to another on the same production line.
In Laboratory Research
Laboratories engaged in either scientific research or process development, never know from one day to the next, what gas mixtures they might need. If they are required to wait for a commercial producer to provide a custom mixture, their R&D timelines would be extended to an untenable degree. Here, small, open-ended gas mixing systems become “Worth-Their-Weight-In-Gold” for creating the blend du jour.
How Do Gas Mixers Work?
Gas mixers generate a controlled amount of each constituent gas to form the desired blend. Commercial gas suppliers of high pressure gas cylinders have a number of different ways to achieve this. Amongst these methods are: partial pressure volumetric mixing, gravimetric mass fraction blending, pressure-swing/membrane reduction mixing, and precision mass control additive blending.
The most advanced gas mixing technology today is mass flow control (MFC) additive blending. A mass flow controller automatically regulates a gas flow to achieve a commanded flow rate. In an ideal world, this would be accomplished by ‘counting molecules’. The closest one can come to this ideal, in the real world, is to use volumetric units of measure over time corrected to standard conditions of temperature and pressure. This should technically be called ‘Molar Flow’ but the industry has settled on the term ‘Mass Flow’. This is considered a ‘true measure’ of gas flow, as the mass of the gas stream will not be affected by ambient pressures or temperatures, unlike volumetric measurements. The result is a more quantitative measure of control for precise gas blends.
Gas mixers with mass flow controllers, themselves can be further broken down into different categories (differential-pressure or thermal-based). In either case, a gas flow sensing element is combined with a proportional control valve and a computational element. This assemblage allows for the manipulation of mass (molar) flow rates. This principle is true whether the sensing unit is a set of piezo-resistive transducers or a capillary tube thermal sensor. With a high speed, closed-loop feedback system, modern MFCs can precisely adjust the individual gas streams which are then combined to create the desired mix ratios.
Our MXM Gas Mixers
Fusion Flow Technologies, a subsidiary of Alicat Scientific, Inc., has designed a proprietary range of gas mixers using the world’s fastest MFCs. These differential pressure based mass flow controllers far surpass their thermal counterparts in terms of speed of response and usable flow range. The results are an accurate and reliable gas blending process, as well as the ability to precisely control flow and pressure without ancillary components.
Fusion Flow Technologies produces a range of gas mixing solutions with its ‘MXM’ platform, with a variety of user-specific features engineered to meet each customers’ unique needs. These fully customized systems may be configured to accommodate as many as ten different gas channels, with built-in support for over 100 common pure and mixed gases per channel and the ability to accept bespoke pre-mixed gas blends a well.
If you would like to learn more about the Fusion Flow Technologies MXM gas mixing solution, please contact a member of the Fusion Flow team today.